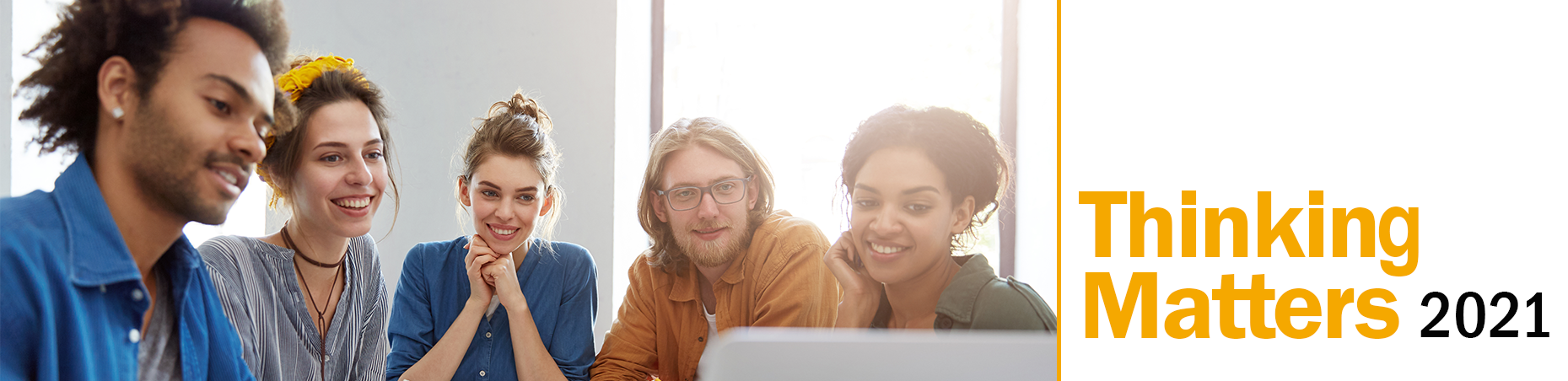
Document Type
Oral Presentation
Department
Engineering
Faculty Mentor
Asheesh Lanba, PhD
Keywords
3D-printing, jacket-structure, mechanical testing, ANSYS, stress testing, additive manufacturing, environmental technology, sustainability
Abstract
Increased clean energy needs have spiked interest in harvesting wind energy off the coast of New England. The region experiences drastic changes in weather patterns from season to season, significantly impacting strength and life of the offshore structures. As 3D printing capabilities improve, the ability to manufacture these large structures is becoming more possible every day. In this study, correlations between full-scale software model testing and 3D printed model testing of offshore jacket structures were investigated. A modern model offshore wind turbine structure was designed and analyzed using carbon fiber reinforced polycarbonate. The tripod-like structure was designed and analyzed using finite element analysis and ANSYS software for both actual size and a model uniformly scaled for printing. The scaled model was then printed using a 3D printer and analyzed with compression testing. Research validation was performed using steel as the common material, proving accuracy of FEA and ANSYS results. Final testing of designs resulted in a better understanding of testing 3D printed materials and improved standards of testing.
Offshore Presentation (UROP 04-15-2021)
TM2021_Rushford-B_transcript.txt (11 kB)
Exploring Possibilities for Scaled Testing of Offshore Jacket Structures via 3D Printing - transcript
Open Access?
1
Exploring Possibilities for Scaled Testing of Offshore Jacket Structures via 3D Printing
Increased clean energy needs have spiked interest in harvesting wind energy off the coast of New England. The region experiences drastic changes in weather patterns from season to season, significantly impacting strength and life of the offshore structures. As 3D printing capabilities improve, the ability to manufacture these large structures is becoming more possible every day. In this study, correlations between full-scale software model testing and 3D printed model testing of offshore jacket structures were investigated. A modern model offshore wind turbine structure was designed and analyzed using carbon fiber reinforced polycarbonate. The tripod-like structure was designed and analyzed using finite element analysis and ANSYS software for both actual size and a model uniformly scaled for printing. The scaled model was then printed using a 3D printer and analyzed with compression testing. Research validation was performed using steel as the common material, proving accuracy of FEA and ANSYS results. Final testing of designs resulted in a better understanding of testing 3D printed materials and improved standards of testing.