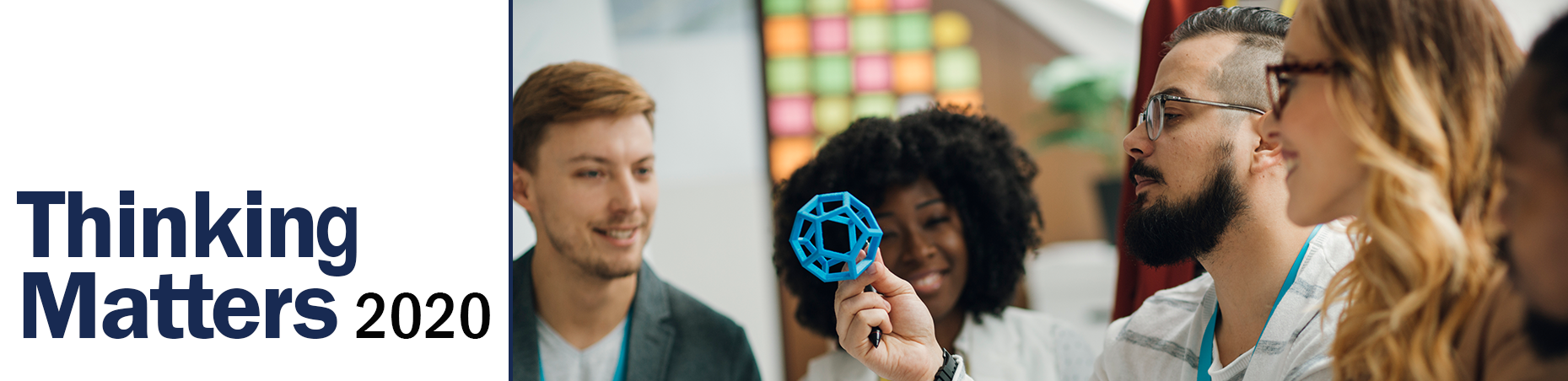
Document Type
Poster Session
Department
Engineering
Faculty Mentor
Asheesh Lanba, PhD
Abstract
The various ways that nature has enabled organisms to perform amazing feats is well known. Materials utilized in the construction of biological structures use only what is available, and with the bare minimum of resources, the bodies of some animals outperform advanced materials made by humans. The Peacock Mantis Shrimp uses its dactyl club, creating devastating cavitation bubbles, to obliterate mollusks and other small arthropods on a daily basis. Despite repetitive impacts and cyclic loading in compression, the body parts of the mantis shrimp continue to allow the animal to feed itself. It is now known that the durability of the mantis shrimp is due to the helically structured mineral biopolymer that its shell is composed of, encasing the animal in what is by all definitions an incredibly advanced suit of armor. Helical layup schedules have proven to be more durable in compression and impact testing than traditional layup schedules with uni- or biaxial fiber orientations. In this study, we create a helically stacked laminate composite in ANSYS using a carbon fiber and epoxy pre-preg (CFRP) material. Tsai-Hill and Tsai-Wu failure criterion for composite laminate are used to determine failure. We perform compression and point force analysis on this composite material and compare its performance to composites commonly used in industry. Composite structures employed in daily industrial applications frequently sustain impact damage; these loadings are constantly present in real world composite employment and frequently result in damage emerging as micro-cracking in the polymer matrix and/or fracture of the fiber tows of the reinforcement.
Open Access?
1
Bio Inspired Composites Perform Better In Compression and Impact
The various ways that nature has enabled organisms to perform amazing feats is well known. Materials utilized in the construction of biological structures use only what is available, and with the bare minimum of resources, the bodies of some animals outperform advanced materials made by humans. The Peacock Mantis Shrimp uses its dactyl club, creating devastating cavitation bubbles, to obliterate mollusks and other small arthropods on a daily basis. Despite repetitive impacts and cyclic loading in compression, the body parts of the mantis shrimp continue to allow the animal to feed itself. It is now known that the durability of the mantis shrimp is due to the helically structured mineral biopolymer that its shell is composed of, encasing the animal in what is by all definitions an incredibly advanced suit of armor. Helical layup schedules have proven to be more durable in compression and impact testing than traditional layup schedules with uni- or biaxial fiber orientations. In this study, we create a helically stacked laminate composite in ANSYS using a carbon fiber and epoxy pre-preg (CFRP) material. Tsai-Hill and Tsai-Wu failure criterion for composite laminate are used to determine failure. We perform compression and point force analysis on this composite material and compare its performance to composites commonly used in industry. Composite structures employed in daily industrial applications frequently sustain impact damage; these loadings are constantly present in real world composite employment and frequently result in damage emerging as micro-cracking in the polymer matrix and/or fracture of the fiber tows of the reinforcement.