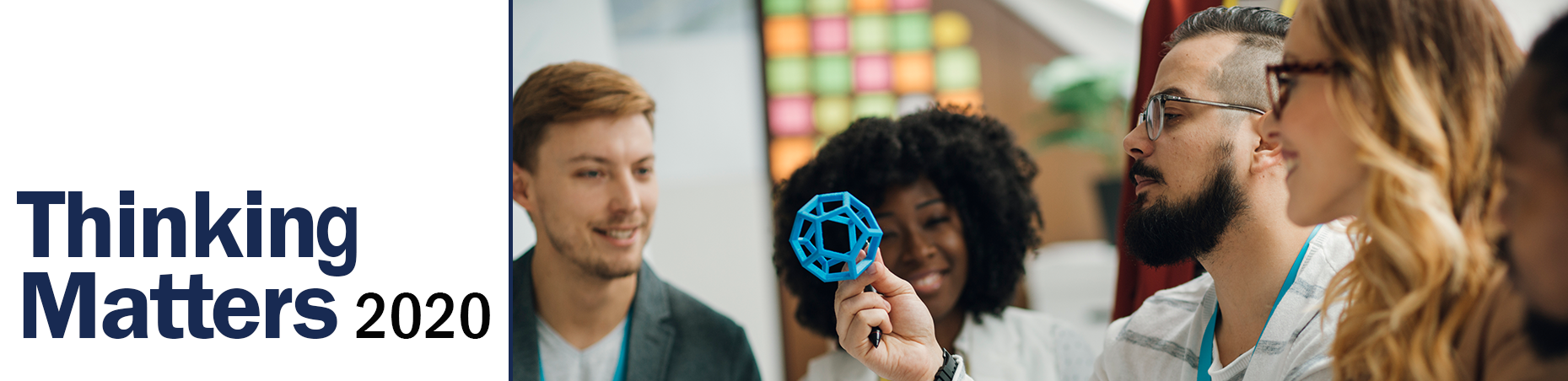
Document Type
Poster Session
Department
Engineering
Faculty Mentor
Mustafa Guvench, PhD
Abstract
The challenging issue in MEMS (Micro Electro-Mechanical Systems) technology development and commercialization is justifying its reliability. Integrating multiple devices on the same chip must handle more failure modes. Some causes for device failures are frequency shifts, wrong modes, structural defects, and lack of reliability. This project focuses on redesign of piezoelectric energy harvesters using Finite Elements Analysis (FEA) tools: ANSYS and SolidWorks. The harvesters were designed in SolidWorks and simulated in ANSYS. The simulation revealed the following first 3 mode resonant frequencies: 214, 298 and 357 Hz for the first, second and third harvesters, respectively. The maximum equivalent stresses were 8.063, 4.694 and 5.015 Mpa, respectively. After the redesign in SolidWorks, simulation in ANSYS, the harvesters were designed in L-Edit, the software utilized for designs to be sent to MEMSCAP for fabrication.
Open Access?
1
Design and Redesign of MEMS Piezoelectric Energy Harvesters
The challenging issue in MEMS (Micro Electro-Mechanical Systems) technology development and commercialization is justifying its reliability. Integrating multiple devices on the same chip must handle more failure modes. Some causes for device failures are frequency shifts, wrong modes, structural defects, and lack of reliability. This project focuses on redesign of piezoelectric energy harvesters using Finite Elements Analysis (FEA) tools: ANSYS and SolidWorks. The harvesters were designed in SolidWorks and simulated in ANSYS. The simulation revealed the following first 3 mode resonant frequencies: 214, 298 and 357 Hz for the first, second and third harvesters, respectively. The maximum equivalent stresses were 8.063, 4.694 and 5.015 Mpa, respectively. After the redesign in SolidWorks, simulation in ANSYS, the harvesters were designed in L-Edit, the software utilized for designs to be sent to MEMSCAP for fabrication.