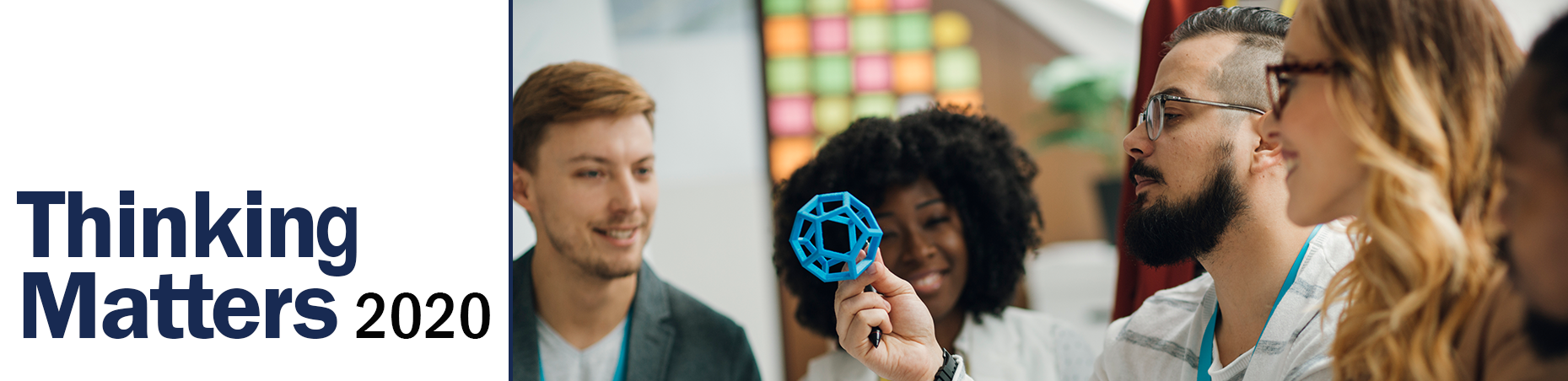
Document Type
Poster Session
Department
Engineering
Faculty Mentor
Michael P. Davis, PhD
Abstract
A system is designed to assess the performance of different rotor shapes under various loading conditions on model wind turbines. Mechanical power converted by the rotor/blades is calculated as the product of the rotor torque and angular velocity. The torque is measured by deflecting a strain gauge plate attached to a permanent magnet dc generator, all of which is mounted in a test stand using ball bearings. The angular velocity is measured via an encoder attached to the dc generator. This measurement of mechanical power is more accurate than measuring the electrical power generated by the dc generator because it is unaffected by electromagnetic losses in the generator.
Under different loading conditions, wind turbine performances vary. To simulate this, the system can vary the mechanical resistance to turning that the rotor experiences by controlling the electrical load on the generator attached to the rotor shaft. Control and data acquisition are done using an Arduino Due microcontroller and the system is interfaced with through MATLAB. This allows for real-time signal processing and a simple user interface with which results can be conveniently view and stored. This will allow for the performance of different rotors and configuration under various loading conditions to be more accurately and completely studied at USM.
Open Access?
1
Measuring the Performance of Model Wind Turbine Rotors
A system is designed to assess the performance of different rotor shapes under various loading conditions on model wind turbines. Mechanical power converted by the rotor/blades is calculated as the product of the rotor torque and angular velocity. The torque is measured by deflecting a strain gauge plate attached to a permanent magnet dc generator, all of which is mounted in a test stand using ball bearings. The angular velocity is measured via an encoder attached to the dc generator. This measurement of mechanical power is more accurate than measuring the electrical power generated by the dc generator because it is unaffected by electromagnetic losses in the generator.
Under different loading conditions, wind turbine performances vary. To simulate this, the system can vary the mechanical resistance to turning that the rotor experiences by controlling the electrical load on the generator attached to the rotor shaft. Control and data acquisition are done using an Arduino Due microcontroller and the system is interfaced with through MATLAB. This allows for real-time signal processing and a simple user interface with which results can be conveniently view and stored. This will allow for the performance of different rotors and configuration under various loading conditions to be more accurately and completely studied at USM.